ODOT 's Preferred Choice For Epoxy Overlay Services
Searching For The Leading Epoxy Overlay Company Trusted By ODOT ?
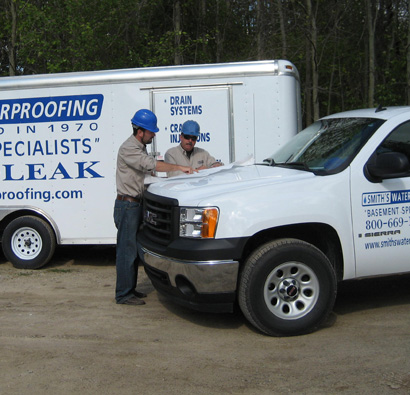
We have worked on over 1,000 bridges in Michigan and the surrounding states for MDOT, counties, and municipalities. We deploy our fleet of vehicles and equipment to jobs across the US, every day of the week.
Our concrete repair team has worked with municipalities to repair cracking concrete on bridges using fibre-reinforced polymer (or FRP) sheets to reinforce structural concrete beams as well as with private industrial clients to remedy problems with their foundation through a variety of crack injection repair techniques. Whatever the size of the job or the nature of the client, the Smith's Waterproofing concrete repair team will bring our decades of experience to the table to ensure that every job is completed properly, safely and on a budget.
Epoxy Overlay Services
A fast and cost effective method of preventative maintenance that includes removing the top layer of concrete from a bridge or road surface, then applying a polyurethane based epoxy and then aggregate. The epoxy enters and seals cracks in the bridge deck and bonds aggregate in place. The aggregate increases vehicle traction and reduces stopping time. Epoxy overlays have been proven to extend the service life of infrastructure and protect investment.
Using Epoxy Overlay for Clarkston Road High Friction Surface Treatment
Oakland County Road Commission chose Smith's Waterproofing to install a high friction surface treatment on Clarkston Road. Work was performed on three specific corners, where multiple vehicular fatalities have occurred. Smith's Waterproofing was the prime contractor for the job and was allowed three weekends to complete the project. The project was completed in just one weekend through great planning and execution by the foremen and crews.
Over 53,150 square feet of high friction surface treatment was installed on Clarkston Road by Smith's Waterproofing. Five shotblast machines were utilized for the surface prep to create a Concrete Surface Profile (CSP) 3 on the road surface, while two crews installed the high friction surface treatment. Smith's also provided traffic control and cleanup services for the project.
- Over 53,150 square feet of High Friction surface treatment installed in a 3-day weekend
- Completed one week ahead of the completion date
- Project complete under budget
- Completed ahead of schedule
- Zero accidents and injuries
Smith's Waterproofing - ODOT 's #1 Name For Epoxy Overlay Services!
High Friction Surface Treatment For ODOT
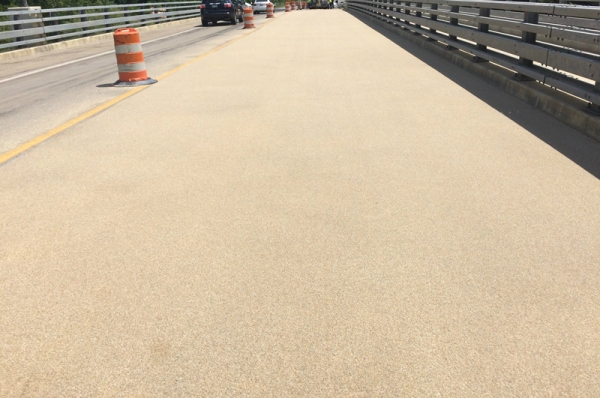
High Friction Surface Treatment (HFST) enhances the ability of a road surface to provide pavement friction to vehicles in critical braking or cornering maneuvers.
- High friction surface treatments dramatically and immediately reduce crashes, injuries, and fatalities. The National Cooperative Highway Research Program (NCHRP) Report 617 indicates a reduction of 20 percent for all intersection crashes.
- Reduce hydroplaning on wet surfaces
- Reduce black ice
Kalamazoo High Friction Surface Treatment:
The State of Michigan and MDOT awarded Smith's Waterproofing the project to install high friction surface treatment on multiple accident-prone locations on the I-94/US-131 interchange, as well as, Gun Lake Casino ramp, Business Loop 94 or US-131, and main line I-94 (near Battle Creek, MI). Each location was chosen due to a fatality, which may have been prevented with a high friction surface treatment.
This project included use of Smith's shotblasting crews to surface prep the areas to a CSP 3 before crews applied the high friction surface treatment. Crews worked around the clock to complete the project, which was in high traffic areas. Night work was required to reduce the impact on traffic and meet the completion deadline.
Smith's setup a temporary yard in Kalamazoo to store trucks, equipment, and material. The temporary yard was strategically chosen in close proximity to each worksite, which increased productivity to meet the project deadline. The location of the shop also minimized time spent traveling to each location and maximized working hours for each crew.
Highlights:
- 218,040 square feet of high friction surface treatment
- Completed 28% under the engineer estimate
- No accidents or injuries
- Completed ahead of schedule
Surface Preparation For ODOT Projects
Combination of methods used to remove deteriorated or contaminated concrete and roughen and clean a substrate to enhance bond of a repair material or protective coating.
Surface Preparation On 1-75:
Through the Michigan Department of Transportation, Smith's Waterproofing acted as the prime contractor on the I-75 High Friction Surface Treatment (HSFT) on I-75 north bound between 11 Mile Road & 12 Mile Road. The project included surface prep of the highway with 5 shotblasters, cleaning the dirt, dust, and contaminants, and then applying the HFST.
Highlights:
- Installation of 58,680 square feet of High Friction Surface Treatment in one weekend
- Setup and maintain traffic control over the entire closure
- Completed 29% under the engineered estimate by MDOT
- Finished project and opened to traffic in less than half of the allowed time
- No reportable injuries or accidents
Healer Sealer and Sealer Overlay Services
See our healer sealer and sealer overlay work in action!
Zilwaukee Bridge -- I-75/ US-23 over the Zilwaukee River
In 2013, the mile and a half long Zilwaukee Bridge was shut down for sealer overlay (healer sealer), structural crack repair to bearing pads, and bearing pad replacement.
Smith's Waterproofing installed sealer overlay (healer sealer) over the entire North and South Bound decks, totaling 1,170,000 square feet. Smith's also performed epoxy crack injection on the bearing pads, which are designed to support up to 8 million pounds each.
Due to the height of the bridge, which reaches 120' at its highest point, boom trucks and snooper trucks were utilized to reach many of the bearing points to perform crack injection. Smith's performed epoxy crack injection on a total of 32 bearing points.
Smith's Waterproofing had limited time frame to complete this project, and performed work in just 15 days during September and October in 2013, and another 15 days in September and October of 2014. This project was completed with no reportable injuries, finished on time, and under budget.