DOT 's Preferred Choice For Polyurethane Crack Injection Services!
Polyurethane Crack Injection Done Right With Smith's Waterproofing!
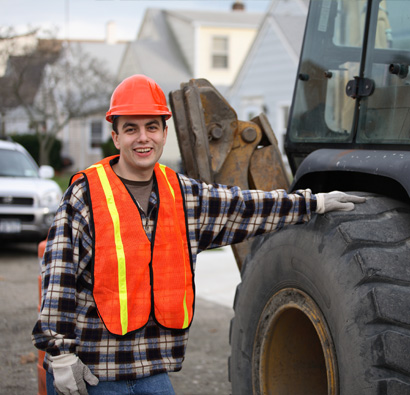
We have worked on over 1,000 bridges in Michigan and the surrounding states for MDOT, counties, and municipalities. We deploy our fleet of vehicles and equipment to jobs across the US, every day of the week.
From commercial clients who require remediation of their concrete foundation walls to municipalities who need a skilled concrete technician to repair and reinforce a bridge's structural concrete beams, the concrete repair teams at Smith's Waterproofing have experience handling a wide range of concrete repairs for a variety of clients. Since our founding in 1970, Smith's Waterproofing has worked hard to earn our reputation as the Midwest's premier concrete repair company.
Whether concrete is deteriorating due to age or new concrete is displaying issues due to poor installation, our expert technicians understand the correct technique to utilize for a long-lasting repair. For example, Smith's Waterproofing performs crack injection repair on new caissons due to water leakage. Whatever the underlying issue, we are able to diagnose the problem and propose a safe, effective and expedient concrete repair solution.
Concrete Repair and Restoration Services For DOT
For this service we remove and replace damaged and deteriorated concrete. Check below to see our team in action replacing and storing concrete on one of our largest jobs yet!
Repairing The Concrete M-20 Over The Tittabawassee River:
The project included patching large amounts of concrete, reinforcing concrete beams with carbon fiber reinforced polymer sheets, structural beam replacement, and adding structural beam stiffeners. Repairs were also performed on concrete column, beams, and the abutments on the bridge.
After concrete was patched, a water repellant coating was installed. Finally, the failing downspouts on the bridge were removed and replaced with Fiber Reinforced Polymer (FRP) downspouts. This was another project completed by Smith's Waterproofing on time, under budget, and without injury.
- Installed structural steel beam stiffeners
- Completed the project ahead of schedule and 10% under budget
- Bike path under bridge was open for duration of project
- News crews and public frequently visited the site for status updates
Structural Crack Repair & Epoxy Crack Injection Services
Injecting epoxy resin into a crack in concrete for restoring structural strength and/ or waterproofing purposes.
Berlin Township Waste Water Treatment Plant:
Smith's Waterproofing was chosen for extensive concrete repair at the Berlin Township Waste Water Treatment plant. The project included concrete structure repair and structural upgrades to the four aeration tanks, aerobic digester tank, distribution tank, and the three clarifier tanks.
Engineers had designed and upgraded the wall design to prevent waste water spills from occurring in emergency flood scenarios. This new design also changed the input of the influent pipe. All four aeration tanks had significant damage from the acidic and harsh nature of waste water. Each aeration tank was drained, and the failing concrete was saw cut and removed around the perimeter. New rebar was installed, forms were built, and the new concrete walls were poured and finished by Smith's crews. The aerobic digesters received similar repairs around the perimeter of each tank. Each tank also received structural epoxy injection to repair all structural cracks. Over 1,000 lineal feet of crack injection was performed.
Each aeration tank, aerobic digester, and distribution chamber had walls with weir plates that were removed and reinstalled with the repairs. This design required Smith's to be within 1/100th of an inch accuracy for the system to operate.
Highlights:
- Tank wall replacement on aeration tanks, aerobic digesters, and clarifier tanks
- Complete demo and rebuild of the distribution box
- Completed job 4 months ahead of schedule and on budget
- All work was performed while plant was in operation
Carbon Fiber Concrete Reinforcement Services For DOT
Stabilizing and repairing damaged concrete and other structures, by installing carbon fiber cloth with an epoxy binder. The process restores the structural and load bearing capacity of the object being reinforced. Can be applied to metal, wood, concrete, or plastic. Has a high strength to weight ratio and quick repair time. Commonly installed on concrete beams bridges, columns, poured in place and precast concrete for maximizing crack control and restoring structural integrity.
Using Carbon Fiber Concrete Reinforcement At The Food Processing Plant:
This project was part of a high efficiency production line upgrade at a food manufacturing plant in South East Michigan. The production line upgrade required the basement foundation walls and bearing walls to be strengthened with carbon fiber reinforced Kevlar.
Engineers determined that the high humidity created by the factory's operating conditions caused large amounts of water to build under the slab of the building. The water created hydrostatic pressure which caused the block walls throughout the building to bow and sheer slide off the foundation.
The solution was three-fold: To eliminate the water below the slab, Smith's added interior drain systems which included industrial sump pumps. Water was diverted to an exterior drain system, which eliminated hydrostatic pressure that was causing walls to bow. Two crews were dedicated to applying waterproof coatings on interior walls and epoxy coatings on the floors. These coating systems were installed to protect the concrete floor and masonry walls from further damage and diverted accumulated water to drain systems.
Masonry and tuck pointing repairs were made to various portions of block walls and concrete walls throughout the factory. After all repairs were made the walls were covered with a concrete texture coating to add a final layer of protection.
The factory remained in operation for the duration of the project. Maintaining strict food safety parameters was a crucial part of this project. Smith's installed a waterproof and dustproof barrier to protect the production line in service.
Highlights:
- Masonry repairs to foundation and walls
- Maintained FDA air quality standards during construction
- Epoxy coatings installed on floor
Polyurethane Crack Injection Services
This process involves sealing or repairing cracks by injecting a polymer or other material for structural repair and/ or waterproofing. Check out our team in action below!
The inspector and engineer onsite acknowledged the high quality of work and after tank coatings were complete, Smith's was instructed to perform crack injection on the caisson as part of a work change directive. Though the caisson was new, it required crack injection at the cold joints where water was leaking through. Smith's utilized a manbasket to inject cracks with both hydrophilic and hydrophobic polyurethane injection grout on the caisson. Smith's also performed polyurethane crack injection on the influent lines to eliminate leaks.
The roof of the caisson received a living roof which allows grass, bushes, and small plants to grow on top of the concrete roof. This particular living roof required a two-part membrane system, with soil layered between each membrane. Smith's was chosen to install the Firestone membrane system, which also included engineered soil and vegetation.
- Vinyl Ester coating protective coating of primary and secondary containment tanks
- Crack injection and waterproofing of caisson and influent lines
- Green/ living roof membrane installation